
Itac employ a variety of testing methods to develop adhesive coating products that align with our customer’s application requirements. These include:
- Adhesive bond strength test (tensile, shear, peel),
- Heat seal testing,
- Drawdown testing,
- Fire retardancy testing,
- Colour testing
- Viscosity testing (Brookfield),
- Solids testing,
- Surface conductivity testing.
Details of the testing standards that Itac work to for each method can be found here.
This area of our work ensures reliability and uniformity in the bonding process within parameters that may also influence performance. These may include consistency of raw materials, application substrates, environmental conditions, and joint design. The results of these tests often support the customer to choose the best adhesive coating system for a specific application. The results can also optimise the formulation process to help ensure we meet product specifications.
We will provide a snapshot of the above adhesive coating testing methods over two instalments. Stick with us and watch this space for part 2!
Adhesive bond strength test (tensile)
Itac conduct adhesive tensile tests to determine the strength of a bond that an adhesive coating provides. This may be between two rigid surfaces, two flexible surfaces, or a combination of both.
The test is known as a “destructive test” and is designed to show how the bond fails under a tensile load as it is pulled apart. The test identifies the weakest part of the bond which can fail in one of three main ways:
- Cohesive Failure where the actual adhesive coating beaks down-the weakest point is within the body of the adhesive;
- Adhesive Failure where the bonded surfaces separate cleanly due to the weakest point being between the adhesive and the substrate;
- Substrate Failure where one or more of the bonded materials breaks down-the adhesive is stronger than the substrate to which it is bonded.
The amount of tensile force that causes the bond to fail is quantified per unit of bonded area. This provides an indication of the bond strength that an adhesive coating provides. Substrate and adhesive materials, adhesive application thickness, and size of the application area are all important variables to observe. Please note that it is the strength of the bond that we measure, not the strength of the adhesive material.
Other measures of bond strength include peel and shear strength. We will visit these when we take another look into adhesive bond strength testing in part 2.
Heat seal testing
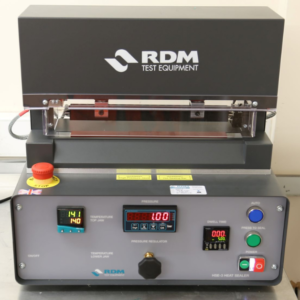
Itac use heat seal testing for applications that require thermally activated adhesives to create the end product, for example, protective laminating films in the print, media, and graphics sectors. The test measures the temperature, pressure, and time parameters for the adhesive to provide optimal heat sealing properties of two similar or dissimilar materials. This helps to customise adhesive solutions that prevent product failure caused by weak seals.
When combined with the tensile tester, the heat seal unit can also be used to make consistently reproducible samples for testing. This is important as bond strength is highly dependent upon how the heat seal bond is prepared.
Drawdown testing
Itac use this laboratory technique to observe the interaction between a flat substrate and coating. Properties such as curing times, wettability, drying weight, and tack strength can be evaluated. These properties are normally determined by the thickness of the coating application. Therefore, an important objective of drawdown testing is to determine the optimal coating thickness required for the specified application. The desired properties for manufacture and end use can then be achieved.
Alike to heat seal testing, drawdown testing can be an important pre-cursor to high quality tensile testing as creating reproducible results requires a consistent amount of adhesive. Furthermore, controlled and repeatable conditions such as speed of drawdown and the size of the gap between the applicator and the substrate, are essential for quality control and research purposes.
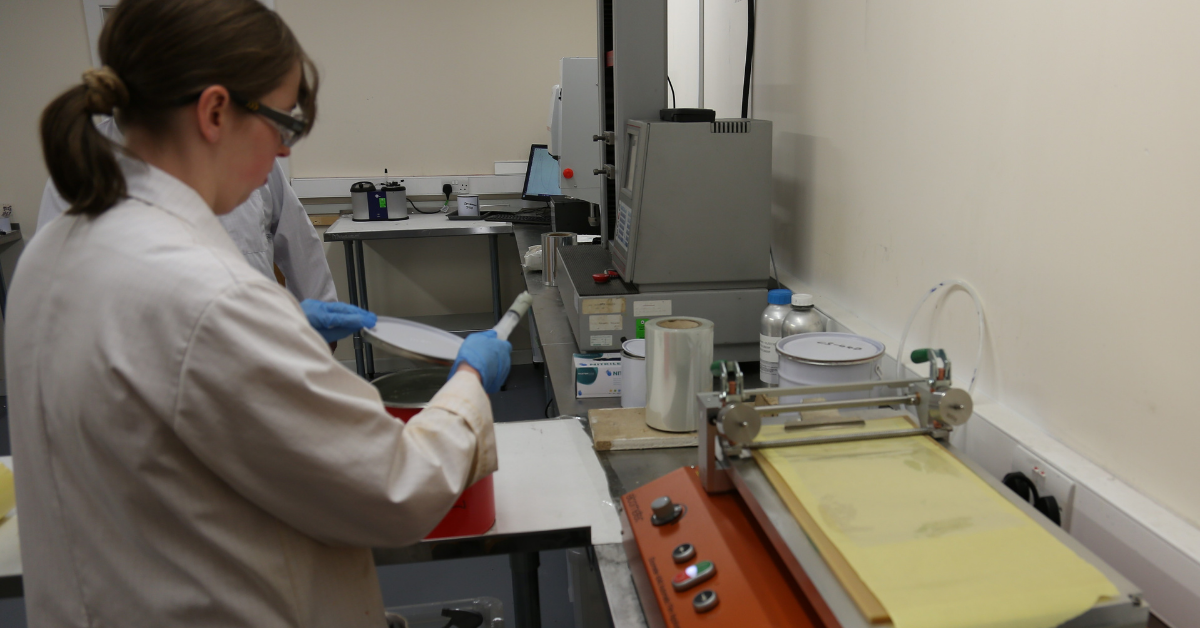
Fire retardancy testing
People often use the terms fire retardant and fire resistant interchangeably, however there is a distinction. Flame resistant materials do not ignite when exposed to a flame or extreme heat due to their inherently natural make-up. Flame retardant materials are chemically treated to protect the substrate by slowing down the spread of flames, and sometimes causing the flames to self-extinguish.
Itac formulate and manufacture flame retardant coatings and test these under controlled conditions to evaluate flame spread or their ability to extinguish the flames once the source of ignition has been removed. There are several factors that can affect this including the application substrate, the thickness of coating applied, and the chemical make-up of the formulation. Itac’s technical team work hand-in-glove with product managers, designers, and formulators to align the above factors with the product specification. This provides effective fire retardant coating solutions that help products meet relevant fire regulations and standards. The ultimate objective here is to provide solutions that preserve life and property in the event of fire.
Read about our intumescent silicone graphite coating here.
Colour testing
Itac use colour testing methods to ensure batch-to-batch consistency and to ensure our coating formulations match the customer’s adhesive coating application requirements.
Due to the different ways people may perceive colours, colour differences, and variations, it is important to categorise them based on their actual properties. Itac prefers to use the CIELAB colour system which offers a standardised and quantifiable measure of colour. This is based on three continuums. These are (L)- light to dark (or white to black known as achromatic colours), (A)- green to red, and (B)- blue to yellow (known as the chromatic colours). The logic behind this method lies in the Opponent Process Theory of Colour Vision which proposes the way humans perceive colour is controlled by the above colour channels.
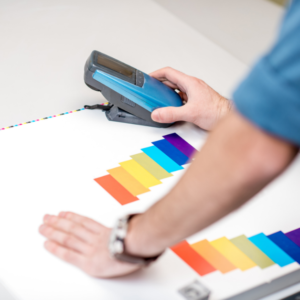
Itac use a Spectrophotometer to determine how far or close the colour of an adhesive coating colour sample is to a specified application colour. It is critical that we get this right, not just for aesthetic reasons, but also for purposes of protection and durability like that required for commercial roof coatings.
We hope you have found this first instalment about Itac’s adhesive coating testing methods informative. If we can be of any assistance for any of your coating challenges, or you would like to see our lab testing in action during a site tour, call us on 01204 573736, email info@itac.uk.com or complete a short enquiry form.
We look forward to hearing from you.