Welcome to part two of our summary of adhesive coating testing methods used at ITAC. We explained in part one that the tests we perform and results we provide are a critical element of our work. These enable our customers to choose the best adhesive or coating system for a specific application, and to help us to optimise the formulation process so we can meet product specifications.
Part two will look at the following coating testing methods:
- Adhesive bond strength test (peel and shear)
- Viscosity testing (Brookfield)
- Solids testing
- Surface conductivity testing.
Adhesive bond strength test (peel and shear)
Part one of our coating testing methods discussion briefly describes how ITAC use the tensile test to illustrate how a bond fails under a tensile load as two surfaces are pulled apart.
ITAC also perform adhesive shear tests which involve applying a parallel force in opposite directions to test the sliding failure between surfaces along a flat plane. The force required to create cohesive, adhesive, or substrate failure is measured. Shear forces exerted on bonded surfaces are one of the most common stresses they need to withstand during their service. This is especially true for structural bonding applications.
Peel tests are typically used when a flexible material is bonded to a firmer surface and the force required to peel the surfaces apart is required. ITAC perform peel tests in different orientations including 90° and 180° as different peeling angles can affect adhesion performance. The bond strength we measure between the surfaces during a peel test may be described as how well the coating has bonded to another surface. Testing for uniformity of adhesion and to specific materials/substrates is often critical for consistency of design and performance.
Viscosity testing (Brookfield Engineering)
The viscosity of a coating explains its thickness and relative resistance to flow. Viscous coatings are thicker and don’t flow easily, compared to those which are less viscous and therefore thinner. The precise viscosity of a coating can determine what method of application is most appropriate, for example, spray, roller, or brush. It also provides information on how much material should cover a given area at the right thickness, and how to prepare coatings prior to application.

ITAC perform tests using a Brookfield viscometer which many consider as an industry standard for measuring viscosity. The Standard Brookfield viscometer test involves immersing a spindle in the coating at a given rotational speed, and measuring the force to keep this speed constant. We then immerse a spindle in the coating at a given rotational speed and measure the force to keep this speed constant. This provides the coating’s viscosity measurement in units of centipoise (cP) and can be an important indicator of how a product will perform during application. The interrelationship between viscosity, the physical characteristics of a product, and the application environment are all important considerations.
Solids testing
Knowing a coating’s solids content is an important factor in calculating its required wet film thickness for application. When we first apply a coating to a surface and it begins the curing process, the coating thickness reduces as solvents evaporate and the solids (resins, pigments, and additives) remain. The quantity of solids which remain on the surace helps to determine the dry film thickness, as well as the thickness of the coating required to provide the coating’s performance characteristics. This is especially important in waterproofing, corrosion resistance, and complex adhesive applications to ensure a quality finish.
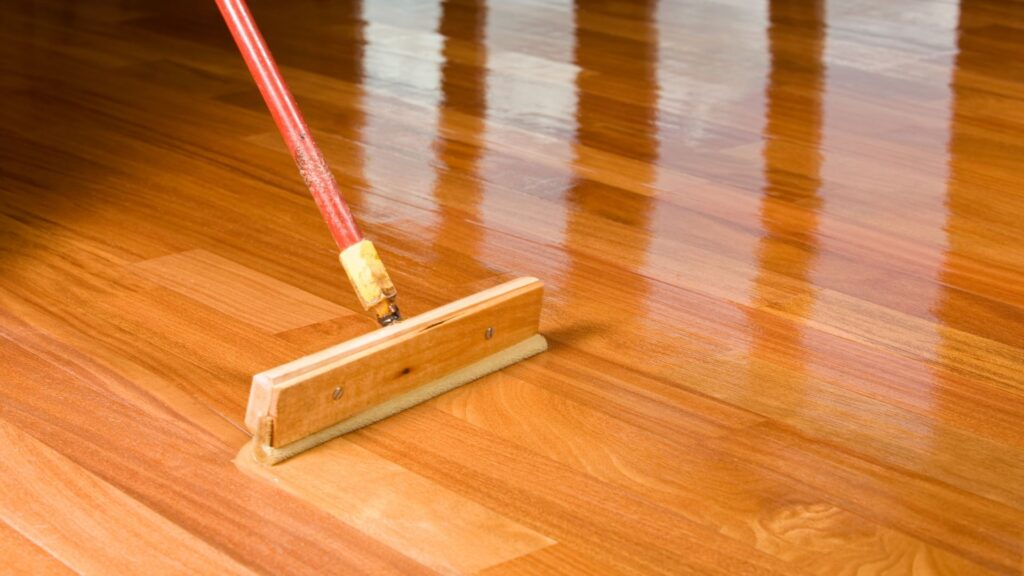
You may be wondering why we can’t just rely on the results from viscosity testing. One reason is that this may only explain how the volume of additives in the coating is affecting its viscosity; not the quality of the coating itself. Solids testing can help solve this problem. This involves heating a sample to remove volatile materials, for example solvents, and measuring its mass loss. The solids content reported can then be used to determine whether a coating is commercially and physically viable for the application or installation scenario.
Surface conductivity testing
Mainly, polymer based coatings are electrically resistive, however, additives can be used in formulations so they become more conductive. For example, conductive additives are commonly used with silicone-based coatings for digester tanks to prevent dangerous build up of static electricity whilst operators work on them.

Prior to application, the coating needs testing to check if the correct level of conductivity is present. Surface conductivity coating testing methods involve passing a small electrical current between two electrodes inside a probe. This connects to a conductivity meter which measures the level of electrical conductivity on a surface when the probe makes contact, and provides an indication of its conductive or insulative properties.
We hope you have found this second instalment about Itac’s adhesive coating testing methods informative. If we can be of any assistance with any of your coating challenges, or you would like to see our lab testing in action during a site tour, call us on 01204 573736, email info@itac.uk.com or complete a short enquiry form.