Since its first use by ancient Maya civilisations, rubber is still an essential polymer for hundreds of everyday products including vehicle tyres, footwear, clothing, sports equipment and kitchen appliances. It is also critical to many industrial and commercial applications such as electrical insulation, PPE, seals and gaskets, hydraulics, rubber drive belts, roof coatings and-yes, you’ve guessed it adhesives!
Rubber is defined as a material which at room temperature can be stretched to at least twice its original length, and after release of the stress it will return to its approximate original dimensions and shape. The rubber used in adhesive glue can either be natural or synthetic. Although both can offer comparable properties, there are several differences to consider before choosing the best rubber-based adhesive for your application.
Natural rubber (NR) adhesive
Natural rubber derives from the latex found in many plants and trees, namely a species called Hevea brasiliensis. Due to its long polymer chains, it has great flexibility and becomes elastic when heated. These properties make NR adhesives particularly suitable for bonding porous materials such as paper, leather and fabrics, meaning that suitable applications include clothing, footwear, carpet backing and packaging. On its own, natural rubber does not have any adhesive properties so synthetic additives and resins are added to create formulations that supply the required properties. For example, varying tack and peel adhesion strengths can be achieved to meet the requirements of pressure sensitive applications. NR adhesive formulations often supply the high first tack, short peel dwell times (time taken to reach maximum adhesion), and residue free removability needed for many tape and labelling applications.
Despite its popularity, NR adhesives do have several limitations. When exposed to hot temperatures (+70°C), the adhesive can permanently soften and lose its adhesion and cohesion strength. Natural rubber also rapidly degrades when exposed to UV which breaks down its polymer chains. Together with oxidation, this causes the adhesive to weaken. Therefore, NR adhesive glue is generally not a suitable solution for outdoor applications. Their low chemical, oils and solvent resistance also mean that natural rubber adhesives may not perform well where exposure to these elements is high.
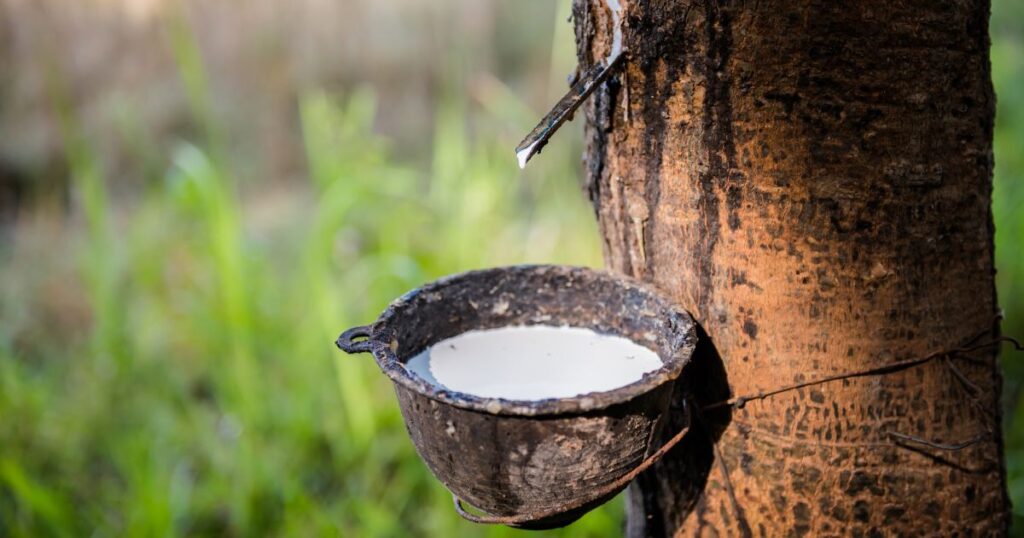
Synthetic rubber adhesive
Synthetic rubbers are manufactured using petrochemical sources in chemical plants, factories and laboratories. Common types include styrene butadiene (SBR), nitrile rubber (NBR), polychloroprene (Neoprene) and silicones. Through the polymerisation of one or more molecular compounds, manufacturers can design and produce products with more complex structures that generally provide greater durability than natural rubbers.
Like natural rubber, synthetic rubbers do not have adhesive properties and additives are needed to create adhesive formulations. However, due to each synthetic rubber having their own beneficial properties, it is easier to develop customised adhesive glue formulations that satisfy unique application and end use requirements. For example, nitrile rubber-based adhesives are known for their high resistance to oils and fuels so are often used for industrial applications such as seals and gaskets. Neoprene based adhesives are characterised by their good resistance to weathering due to their tolerance of moisture, temperature extremes, ozone, UV, and oxidation. These properties together with their chemical stability, make them suitable for a wide range of outdoor applications.
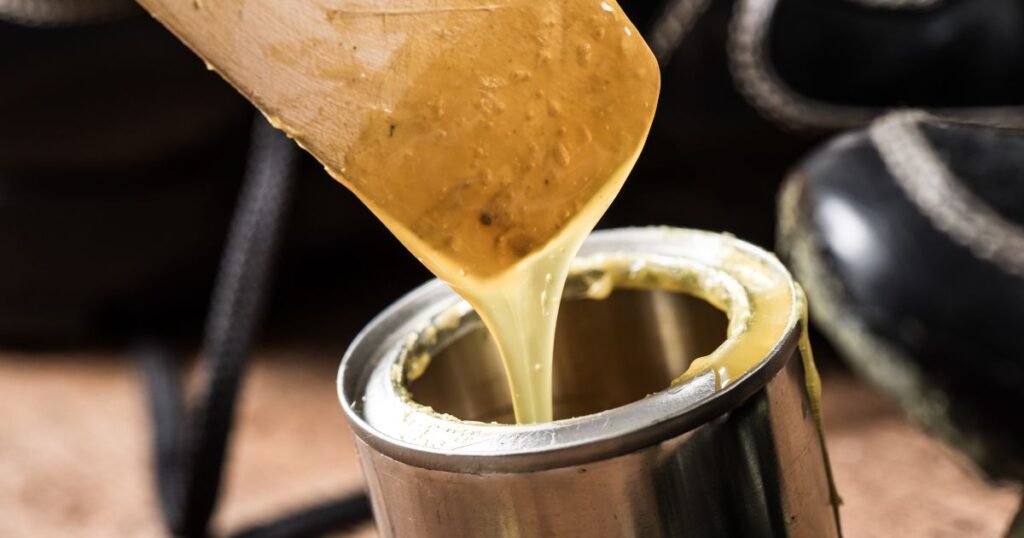
Whilst they might outperform natural rubber adhesives in terms of durability and versatility, synthetic rubber adhesives are generally more costly to manufacture. Costs aside, the decision between which type is more suitable should always be figured out by the substrates to be adhered, the performance requirements of the end application, the specific environment it is expected to perform in, the production environment and the chosen application method. Once these factors have been considered, it may be possible that with the right choice of additives, a natural rubber adhesive can be formulated to meet application requirements.
We have a dedicated sales and technical team at ITAC who can provide advice on the right adhesive glue formulation for the development of high performance products against specification requirements. Talk to us on 01204 573736, email info@itac.uk.com, or complete a simple contact form here.
We look forward to hearing from you.