In 1902, and long before polyurethane adhesives and coatings were known of, ITAC’s founder John Marcus, discovered tyre scrapings dissolved in solvent made an excellent rubber adhesive. When painted on to the outside carcass of a tyre, this formed an ideal primer coat to which the tyre tread could be bonded. This marked ITAC’s beginnings as the “Indian Rubber & Tyre Company”. However, developments in tyre manufacturing eventually resulted in the company needing to find a new outlet for its products, and in the 1930’s ITAC found opportunity in Manchester’s raincoat industry. To be fully waterproof, the seams of coats required treating with a varnish like coating covered with a piece of tape made from the same material as the coat. ITAC thrived with this until World War 2 when materials diminished.

It was not until 1954 that polyurethane technology was introduced to the business. ITAC mixed polyurethane granules with solution which was then sold on to the textile clothing industry to provide a waterproof coating for sector’s end products. When applied to fabric, the coating solution dried to a tack-free film to render the whole garment waterproof, not just the seams. From there, ITAC’s performance coatings and adhesives portfolio has grown to provide an increasing array of effects that provide solutions to many problems within and between industries. From chemical resistance properties to varying tack and grab strengths, this growth can be largely attributed to the evolution of polyurethane technologies and associated capabilities.
Polyurethane has been described by many as a material that defines the word versatile! Isocyanates, the chemical blocks that form part of a polyurethane’s makeup, along with the polyols they are combined with, are wide and varied. Consequently, the polyurethane-based materials produced to address specific requirements can be equally diverse. This provides manufacturers with opportunities for customisation; a core competence essential for successful business transactions and relationships. This versatility can be further enhanced by using additives, modifying processing techniques, and improving formulations through effective R&D. With polyurethanes the possibilities seem limitless, which makes it the material of choice for many applications.
Adhesives
Polyurethane-based adhesives can be precisely formulated to meet a product’s specific requirements, and also modified to provide the required performance characteristics for another. For example, due to the reactivity of the isocyanate component in the polyurethane, fast cure rates can be obtained in applications such as structural joints. However, this can be slowed down where required through altering the level of catalysts used in the formulation.

Polyurethane-based adhesives can be used to provide strong bonds between different material substrates for example, metal, plaster, cork, plastic, and wood. They are therefore highly sought after in the construction, automotive and aerospace industries where such a versatile range of materials are used. Their excellent bond properties also make polyurethane-based adhesives suitable for the manufacture of various types of packaging where resilience and strength are key factors in the safe transportation, storage, and display of finished goods.
Coatings
Performance coatings are normally designed to have a decorative or protective purpose, or often both. They can increase product lifecycles, enhance appearance, and facilitate ease of use and maintenance for the end user. Polyurethane-based coatings form a large part of material engineering from consumer goods sectors to construction, aerospace, and civil engineering.
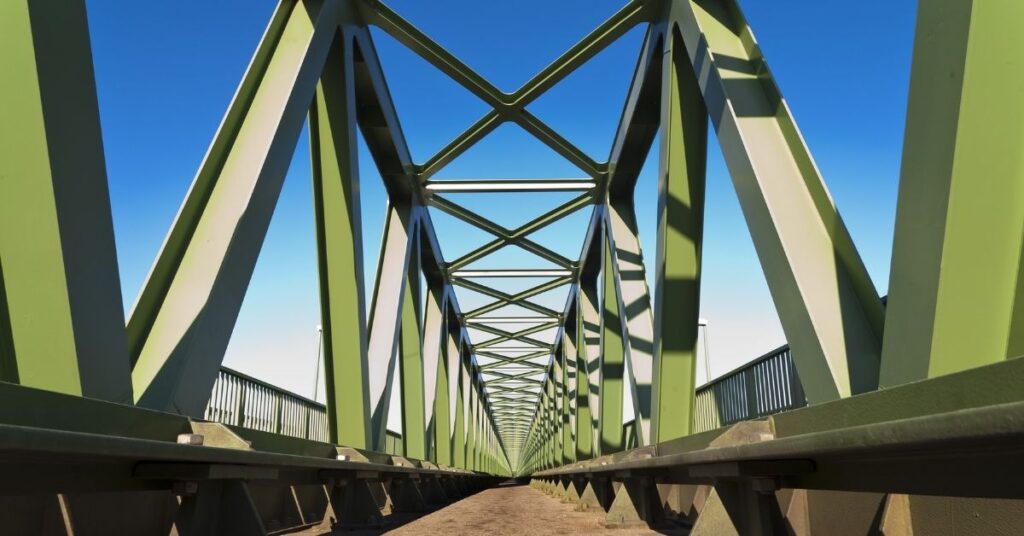
Like adhesives, polyurethane-based coatings are extremely versatile in their application due to their multifaceted properties. They are formulated with either aromatic or aliphatic isocyanates, the latter being preferred for more demanding applications where strong resistance to oxidation, UV radiation, temperature extremes, and pollution are required. Due to their durability, versatility, and practicality, polyurethane-based coatings hold a large portion of market share within the performance coatings sector.
ITAC recognise that one adhesive or coating does not fit all. Further information on ITAC’s technical solutions and application expertise can be found by calling 01204 573736 or emailing info@itac.uk.com. Alternatively complete a simple contact form and we will get back to you soon.