Specialist coatings play a critical role in satisfying the requirements of an ever-increasing number of industrial and commercial products and systems. The coating’s end application and intended use determines the effects it should impart in order to provide the desired performance. This clearly has a direct influence on their formulation design. Therefore, for specialist coatings to be successful, the properties of the colour pigments used for their formulation and manufacture must also be fit for purpose. The chemistry between the two must align to achieve the quality and overall purpose of the coating.
The purpose of specialist coatings vary greatly for products and systems within and between industries. Their formulations may be designed and manufactured to have protective, aesthetic, or functional properties; or indeed any combination of these. Protective coatings may include those that provide, for instance, corrosion, abrasion, and UV resistance to promote durability. Aesthetic coatings applications are for decorative purposes to enhance an item’s appearance or make it visually appealing. Functional coatings fulfil a specific role, for example, making a conveyor belt food contact safe through anti-microbial properties. Colour coatings can also provide a visual reference such as for gaskets to guide correct usage in industrial settings.
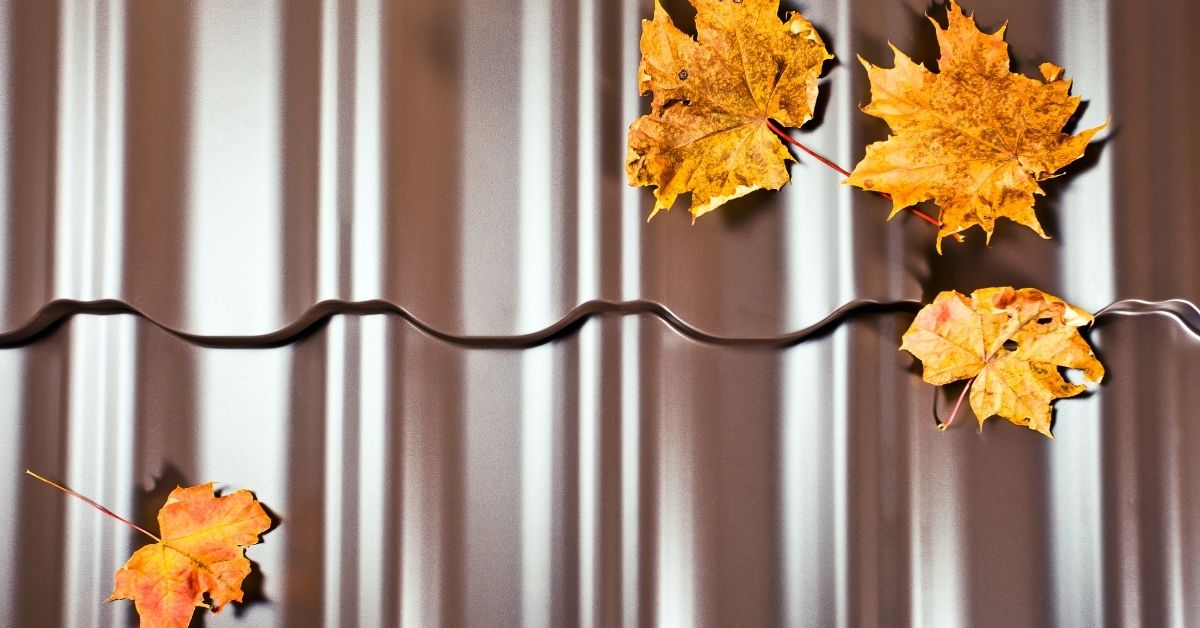
Colour pigments
When choosing a colour for specialist coatings, it is important to consider the inherent properties of the pigment. For example, brown pigment- calcium plumbate might be a good option for an anti-corrosion coating applications on steel structures. This is due to the pigment’s anodic protection properties which enable oxidisation of soluble iron compounds to restrict corrosion. This pigment also supports good adhesion and overall durability of the coating.
Below you will find more examples of some common colour pigments and why they may, or may not, be suitable for your specialist coatings formulations. It is important to note here that pigments can be organic or inorganic in their composition. The focus here is on the latter due to their wider industrial and commercial application.
Blue inorganic pigments
Due to its excellent solvent, heat, and fade resistance, ultramarine blue is a popular pigment for specialist coatings applications in a variety of sectors including packaging, graphics, automotive. and construction. The pigment’s low toxic properties also make it ideal for coatings in the manufacture of toys and food contact plastics. Despite these strengths, some applications may see poor wetting performance without the use of additives.

Red inorganic pigments
Cadmium red pigment is common in specialist coatings for a variety of materials including plastics, metals, ceramics and glass. They enable high temperature resistance during manufacturing processes – ideal for the glazing and firing of cookware, dinnerware, and other ceramics. Industrial coil coatings are another common application, together with applications that need to withstand processing temperatures of 400°C and above.
Green inorganic pigments
Chromium oxide green pigment, (not to be confused with chrome green pigment), enables excellent weatherability including solvent resistance, heat and chemical stability, and UV resistance. Due to their outstanding durability, these are a good choice in the building and construction sector for applications such as roof coatings and floor coverings where colourfastness is an important property.
Black inorganic pigments
Carbon black pigment can be used in coatings to provide a variety of effects for the end application. One of its popular uses is as a conductive additive in static dissipative coating formulations. These can provide protection against dangerous build up of static in environments where gases are present, hence reducing the risk of explosion. When not for a conductive additive, carbon black is also ideal for industrial coating formulations where very low viscosity is a requirement.
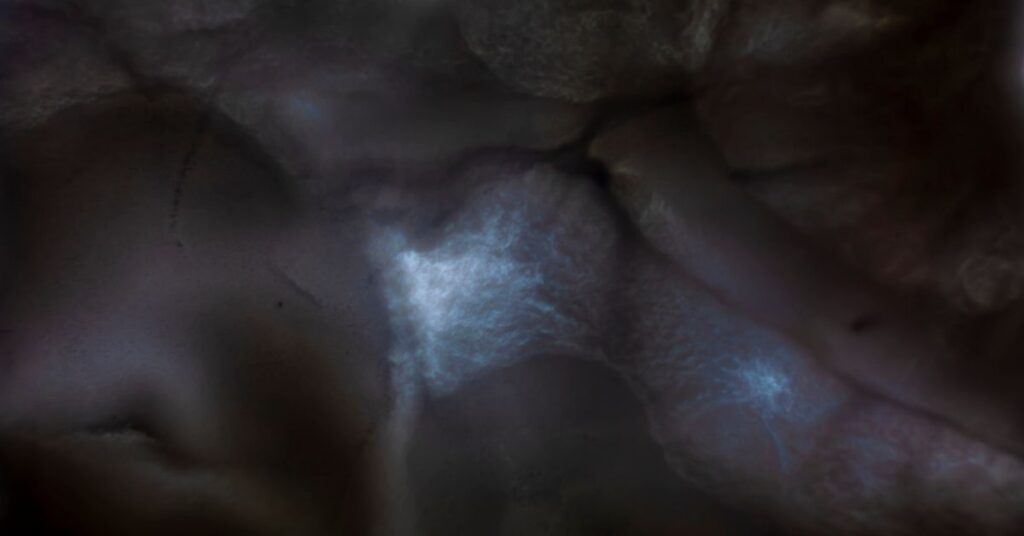
Yellow inorganic pigments
Yellow pigments provide specialist coatings with varying levels of shade, opacity, and colourfastness. For example, lead chromate yellow pigment coatings are prone to fading due to their poor resilience to acids and alkalis. Yellow oxide pigments have high resistance to chemicals and solvents, yet limited heat stability. The latter are suitable for non-aqueous coatings for general industrial and maintenance finishes.
White inorganic pigments
The most prevalent white pigment is titanium dioxide which provides specialist coatings with good chemical, solvent, and heat resistance, and therefore offers suitability for most industrial and building applications. Coatings with titanium dioxide are also common in food packaging and the manufacture of toys due to the pigment’s non-toxic properties. Other, less common inorganic white pigments include zinc oxide, zinc sulphide and lithopone.
This short article has discussed some of the factors to consider when choosing the best colour for specialist coatings. However, a much deeper appreciation of the chemistry behind this is essential to ensure successful and effective alignment with the application and its performance requirements.
This is where ITAC come in. By working in close partnership with our customers, we align the chemistry with the application to make their products work how they want them to work! If this sounds like something we could bring to your table, we would be delighted to hear from you! Call 01204 573736 or email info@itac.uk.com for more information.