Additives are an essential part of coating applications for many manufacturing processes and end products. If added to a formulation, a solvent can manipulate properties to provide a ‘customised’ coating solution. This action results in additional functionality that many alternative coating technologies cannot match in terms of manufacturing capabilities or the specific performance properties of the finished product. Additives for coating applications may include:
- Solvents
- Catalysts
- Extenders
- Thickening agents
- Levelling agents
Solvents
Solvents are substances capable of dissolving other substances to form a solution. They are used in coatings to disperse the various components of a formulation (e.g., pigments, binders) before the product is applied. Solvents also control the viscosity of the coating for the required substrate and application method. If a coating is applied to a substrate, the solvent evaporates, thereby leaving the resin and pigments to form a film that has a consistent appearance and quality.
Due to their release of volatile organic compounds, the aim is to reduce the amount of solvents in coating applications. However, their rapid drying times, durability and ability to withstand harsh environments and temperature extremes make solvent-based coating applications the most workable option for many products and manufacturing processes.
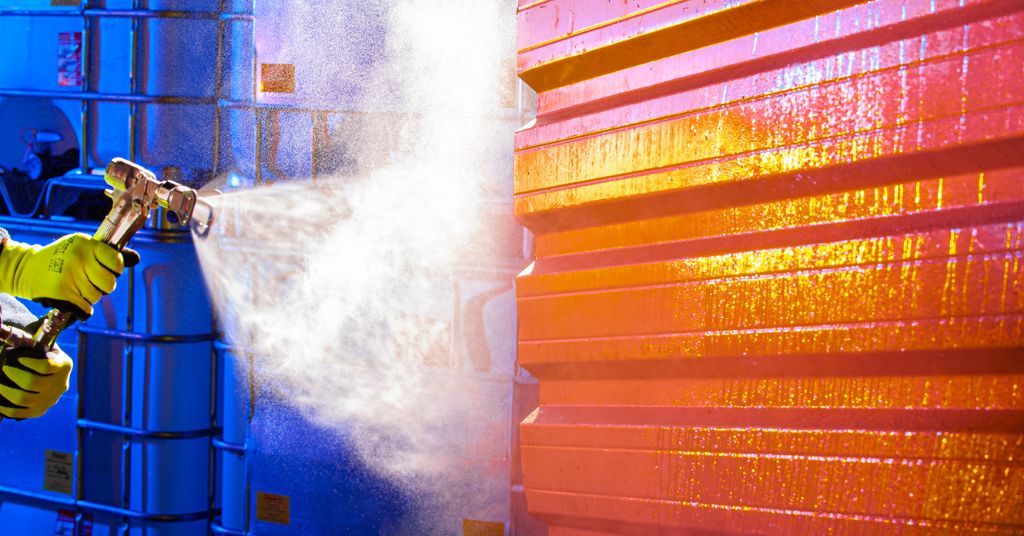
Catalysts
A catalyst is a substance that speeds up a chemical reaction without being consumed in the process. Catalysts are added to coating formulations to: (i) influence their reaction rates during polymerisation; (ii) provide beneficial properties to coating applications. A typical example is faster reaction rates enabling quicker drying times at lower temperatures while providing enhanced mechanical properties and durability. These actions permit productive and cost-effective coating applications, higher-quality coatings and, therefore, better-quality finished products.
Obviously, this is a simple explanation. Important considerations include the: (i) compatibility of the catalyst with the coating formulation; (ii) toxicity of chemicals used in some catalysts and their implications for human health and the environment; (iii) expected or required pot life of the coating product before application.
Extenders
Extenders are substances added to a material to increase its volume or bulk without altering its properties significantly. They are used in coatings to enhance performance before, during and after application. Magnesium silicate (‘talc’) is a good example. Talc is added to formulations to increase viscosity and create the appropriate levels of coverage and dispersion upon application. After application, the talc in the coating creates a barrier against moisture and chemicals due to its hydrophobic properties. This feature protects against corrosion, peeling and cracking of the coated surface.
Another example is the inclusion of extenders to increase the pot life of a coating. This is achieved by the extender maintaining the coating at the correct application viscosity for longer periods, thereby reducing costs and waste.
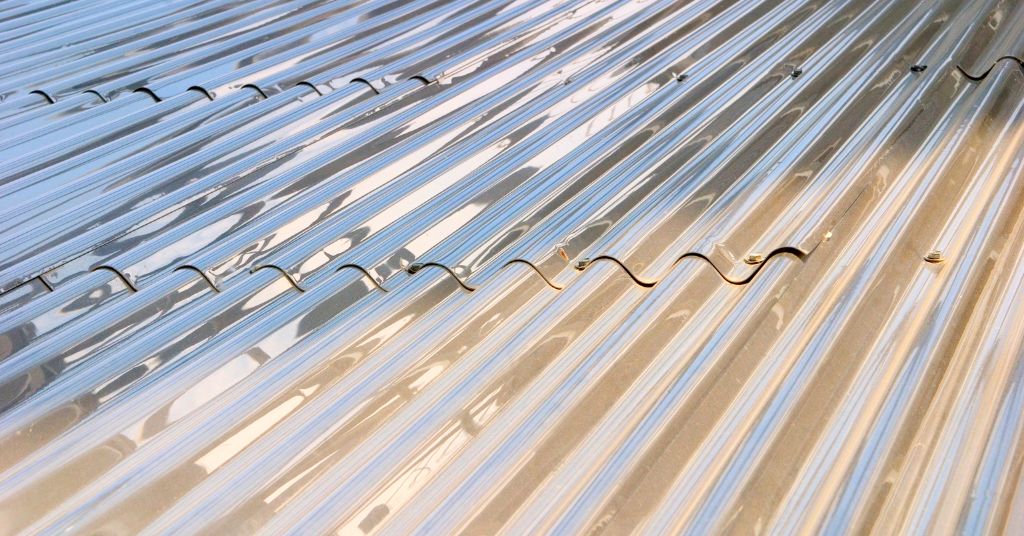
Thickening agents
A thickening agent is a substance that increases the viscosity or thickness of a liquid without altering its other properties substantially. Thickening agents (also termed ‘rheology modifiers’) are added to coating formulations to provide the requisite flow properties. These can be pseudoplastic or thixotropic. The former is characterised by increased viscosity as force is applied, and the latter is characterised by reduced viscosity. These factors are crucial to the chosen application method and outcome of the finished product. For example, the correct viscosity upon application can prevent excess dripping/spattering if a brush or roller is used, and can promote a consistent and durable finish. Thickening agents can also be employed to promote the correct rheology characteristics required of a coating formulation throughout manufacturing, storage and transportation.
Choosing the optimal thickening agent involves consideration of the composition of other components in the coating formulation (base polymer, solvents, pigments and other additives). Common thickening agents include polyamides, fumed silicas and hydrogenated castor oils.
Levelling agents
Levelling agents are chemical additives used to promote even distribution of a liquid substance over a surface during application. If aesthetics are important, they can be employed to optimise the finished appearance of a coated surface. Levelling agents control the surface tension of a coating (i.e., its ability to wet and spread adequately over a given substrate). If the surface tension of a coating is too high, defects which may not have been visible upon application may appear once the coating has dried. Defects can include pinholes, scratches, craters, “floating” and “flooding”. Levelling agents are added to coating formulations to help eliminate these surface defects and provide a superior looking and smoother appearance.
Levelling agents are very common in applications such as automotive spray-coating, wood finishes, industrial metal coatings as well as coil and extrusion coatings.
Additives comprise only a small proportion of all the components in a coating formulation. However, the performance characteristics they enable are very important for manufacturing, storage, application and/or end-use stages. Hence, consideration of the most appropriate additives is crucial.
ITAC leave no stone unturned in selecting the best materials for your coating application before using our specialist compounding expertise to create the perfect formulation. Make an enquiry today by completing a simple contact form or by emailing us at info@itac.uk.com. We look forward to hearing from you.