Specialist adhesives consist of a variety of chemistries and come in a range of forms to suit specific requirements. Choosing the right adhesive formulation for a particular problem or application involves careful consideration of a number of factors. These include:
- Bonding properties of the adhesive
- The application and substrate type
- Application methods and production requirements
- End use environment and performance requirements
It is worth noting here that there is some overlap between these factors as they can be interdependent. For example, on porous surfaces, the success of the formulation may depend on the adhesive achieving a high degree of penetration into the substrate. In contrast, on non-porous surfaces, the use of a primer or surface modifier may be required to increase adhesion.
Let’s take a look at each variable in closer detail.
Bonding properties of the adhesive
Specialist adhesives can be formulated to provide a strong, immediate, and permanent bond between two surfaces, or a bond where the surfaces can be separated and repositioned before the optimal bond is achieved. The first may be suitable for activities where fast application is needed such as automated vehicle production assembly lines. The latter would be useful further down the production line such as where vehicle wrapping films are applied.
Adhesive strength is a major determinant for the reliability of the bond formed between two substrates, as well as its performance during the end application. Specialist adhesives can be formulated to maintain their adhesion under different kinds of stresses, for example, peel, shear and tensile strength. However, the chemical composition and internal cohesive strength of the adhesive, along with it’s ability to remain intact under stresses, also determines adhesive strength. Both adhesive and cohesive failure can cause breakdown of the bond and hence product failure.

The application and substrate type
To achieve the required bond, the substrate material must be compatible with the specialist adhesives being applied. An adhesive may interact with varying surfaces differently, and so may perform better on some than others. Therefore, knowing the exact material of the substrates to be bonded is essential. This is especially true when thinking about generic terms such as metals and plastics as both include a number of different materials. For example, some plastics do not tolerate high temperatures. Therefore, careful thought about the adhesive’s curing characteristics and requirements are needed. An adhesive that bonds well to stainless steel might not give the same characteristics when applied to aluminium. In every case, the adhesive formulation needs to be tested against the specific application substrate.
Other considerations for adhesive compatibility include the condition and size of the application surface. For example, its cleanliness, porosity, flexibility and how rough or smooth it is. Surface preparation guidelines in terms of these factors should be reviewed prior to application. This is to ensure the right formulation is used to maximise the adhesives ability to wet out the bonding substrates. In turn, this optimises contact of the adhesive to the substrate for effective adhesion.
Application methods and production requirements
There are occurrences when specialist adhesives are approved for their end use performance without enough consideration to their suitability at the production stages. This often leads to both financial and timely losses due to wasted materials, down time, and production delays. These all have a knock-on effect for those further along the supply chain and ultimately, the end consumer. Factors such as the application method, curing environment and duration, storage, handling, and disposal of product are all critical considerations. For example, the viscosity of an adhesive formulation may be too thin or thick to be applied using the specified application method, or some substrate materials may not be able to withstand high temperatures which are necessary to cure the adhesive.
Environmental conditions necessary for effective application are also a factor. For example, small changes in temperature can affect cure rates and moisture caused by humidity can result in the desired bond strength not being achieved. Cleanliness may need careful consideration, especially for medical adhesive applications where risk of contamination must be eliminated. A substrate’s exposure to chemicals and outgassing can affect its ability to bond if sensitive to these. The list goes on and, where applicable, successful application is dependent on effective management of these environmental factors.
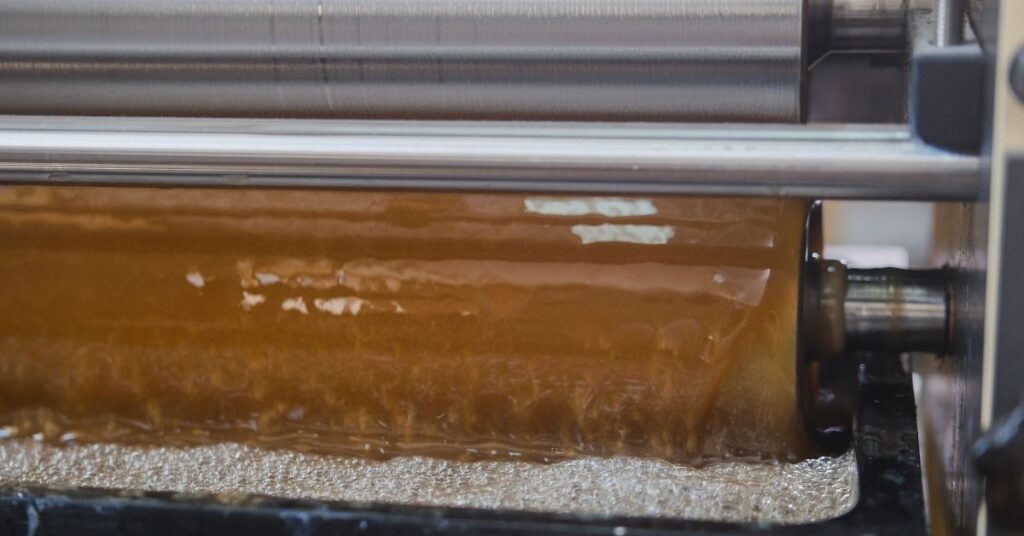
End use environment and performance requirements
There are numerous environmental conditions which can affect an adhesive’s end use performance. These may include exposure to temperature extremes and variations, moisture, UV radiation, chemicals and gases, and mechanical stresses. Temperature is often regarded as one of the most critical environmental factors. For example, specialist adhesives used for external or industrial applications may experience extreme temperature variations and must be able to expand and contract with the bonded substrates.
The property that can provide an indication of how well an adhesive will withstand temperature variations is its glass transition temperature (Tg). This tells us the temperature at which the mechanical and physical characteristics of the adhesive to starts to change. When an adhesive is above it’s Tg, it’s polymer chains can start to move causing it to soften and become more flexible. The stresses from this continuous softening and hardening can cause an adhesive bond to fail prematurely of the application’s expected lifecycle. To avoid this, specialist adhesives that need to withstand temperature variations should be formulated to have a Tg greater than the environmental temperatures it is expected to perform in.
We hope this snapshot of the main considerations for choosing the right specialist adhesives for the right application has been useful. Of course, the chemistry is actually far more complex than this, but we have a team of experts here at ITAC who can provide the necessary help, advice, and guidance. To contact us, please leave your details here, call us on 01204 573736, or email info@itac.uk.com.
We look forward to hearing from you.