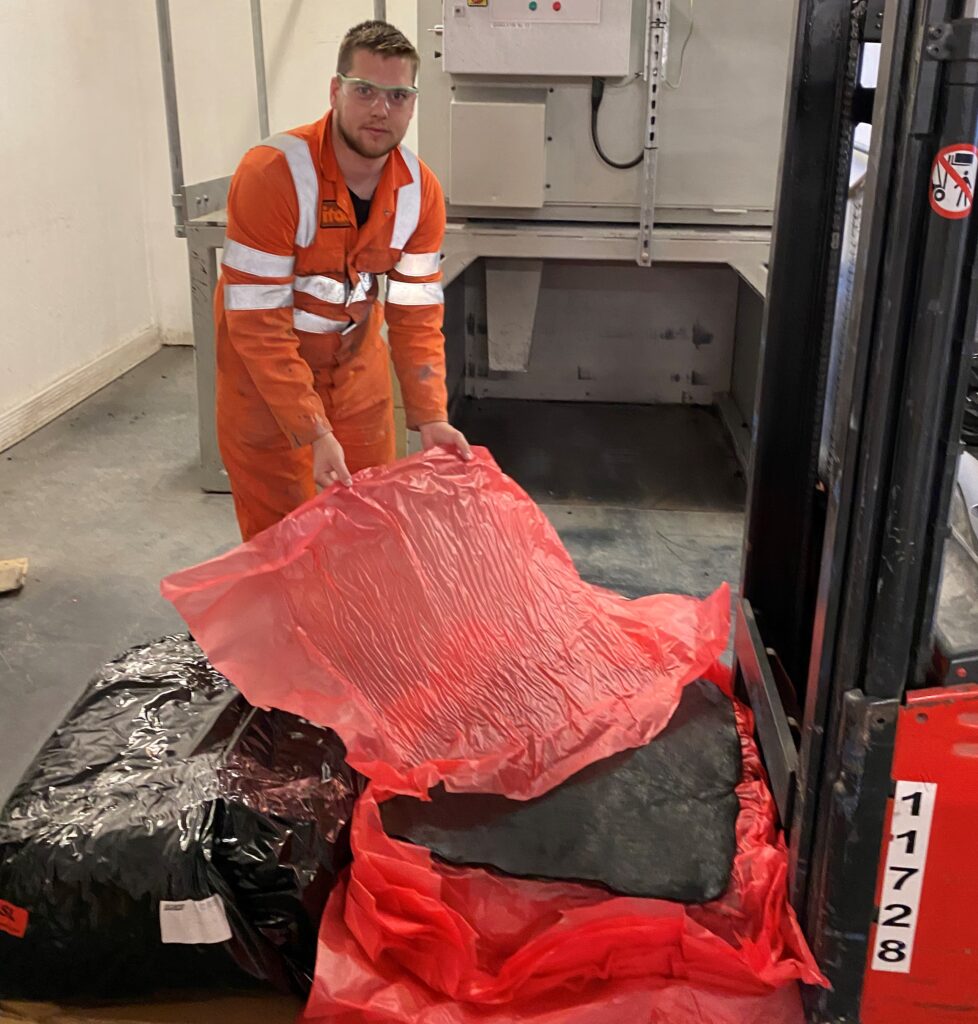
Over the last year, Itac and their manufacturing partner have prevented up to 30,000 large plastic interleaves from going to landfill. This has been made possible through a mutually agreed recycling initiative to reduce plastic waste in their manufacturing processes.
To offer some perspective, 30,000 sheets is enough plastic material to cover the area of 4 football pitches, 24 Olympic-sized swimming pools, or 115 tennis courts! The initiative is part of Itac’s commitment to reducing waste and limiting the possible harmful effects of its business activities on the environment.
By the end of 2020, researchers claim that more than 850 million tonnes of greenhouse gases will have been released into the atmosphere as a direct result from producing and incinerating plastics. It is predicted that these emissions could rise to 2.8 billion tonnes by 2050. These greenhouse gases including Carbon Dioxide, Methane and Ethylene, pose a great risk to global warming and the effect it is having on our planet due to climate change. As the Earth’s surface becomes warmer, the increasing heat leads to more plastics breaking down into greenhouse gases and the further acceleration of climate change. The result is a perpetuating vicious cycle that has reached crisis point, even for many earlier climate change doubters. One scientist has alarmingly pointed out, that when the Earth last had similar concentrations of Carbon Dioxide in the atmosphere, temperatures were 2-3°C warmer and sea levels were 10 – 20 metres higher!

Increased pressure from environmental groups, recent natural disasters, and increased environmental awareness has pushed climate change further up the agenda as a major global concern. The general consensus is that society must do more to ensure plastics are reused wherever possible to prevent them being dumped in landfill or spilled into the seas. This includes the ways in which we do business.
The plastic interleaves are a crucial component in the manufacturing process as they stop the raw materials required for production from sticking together in storage, transit, and handling. Itac are unable to use alternative partitioning techniques for the process as this would affect the compounding process and the quality of the end product. Therefore, the decision was taken to work with their manufacturing partner on a systemised process where the plastic interleaves could be returned for timely reuse.
Operations Director for Itac, Paul Dunkerley, comments:
“It made perfect sense. Having more plastic interleaves manufactured from scratch results in higher costs, so savings were to be made. However, the cost savings made through recycling pale into significance when compared to the long-term impact on the environment if we chose not to pursue this greener initiative”
Itac are now working to the latest ISO 14001 standard and achieved an outstanding result for their most recent external audit in July with no issues raised. Through their environmental policy and environmental management system, Itac continue to pursue improvements in environmental performance by reducing waste, increasing reuse and recycling.